Bát Tràng Ceramic is one of the renowned traditional craft villages in Vietnam, situated along the banks of the Red River, more than 10 km southeast of the center of Hanoi. The Bat Trang ceramic village has a history dating back to the 14th century, closely intertwined with the development of ancient Thang Long.
Bat Trang ceramics are primarily crafted from white clay, known for its high resistance to temperature and impact, vibrant colors, and diverse patterns, making it highly favored by customers both domestically and internationally. With a wide range of products such as Bat Trang teapots, decorative items, prosperity-bringing vases, plates, and bowls, Bat Trang ceramics offer diversity to meet various preferences.
Bat Trang Ceramic possesses numerous advantages compared to other types of ceramics, stemming from its rich historical development and the continuous improvement of products by skilled artisans. The following are some notable advantages of Bat Trang ceramics.
Let’s find out about Advantages of Bat Trang Ceramic with CeramicVietNam.
What is Bat Trang ceramics?
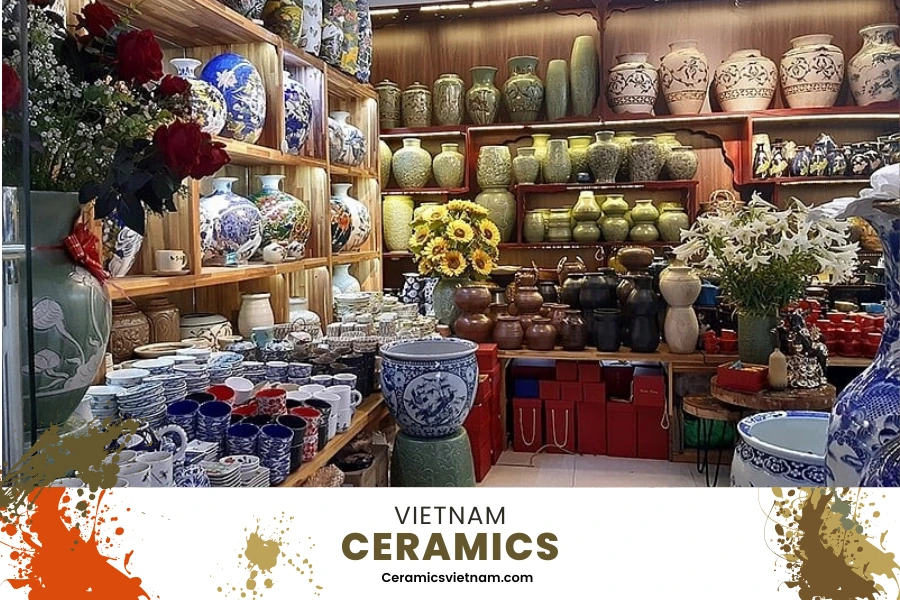
Advantages of Bat Trang Ceramic
Bat Trang Ceramic is the common name for various types of Vietnamese ceramics produced in the Bat Trang village, located in Bat Trang commune, Gia Lam district, Hanoi. In Sino-Vietnamese terms, the word “Bat” (鉢) refers to the alms bowl of a Buddhist monk (in Pali, it is called Patra), and “Trang” (場, also read as Truong) means “a large yard” or “specialized area.” Therefore, the name Bat Trang can be understood as “a large yard specialized in producing bowls.” However, according to some other sources, the name Bat Trang may originate from the name “Bach Tho Phuong,” meaning “the neighborhood of white clay.”
Bat Trang ceramics are exported to many countries, including Japan, South Korea, Europe, the United States, and various other nations. Bat Trang has become a famous tourist destination, attracting both domestic and international visitors for sightseeing, shopping, and experiencing ceramic making. On December 20, 2019, the Ministry of Culture, Sports, and Tourism of Vietnam announced that the pottery craft of Bat Trang village is recognized as a national intangible cultural heritage
Advantages of Bat Trang Ceramic
- Durable construction:
- The high durability of Bat Trang ceramic is a distinctive feature attributed to the structural composition of the ceramic bone. This structure allows products from the Bat Trang craft village to withstand impacts and high temperatures remarkably well. You can confidently place Bat Trang household ceramic products, such as plates and bowls, in the microwave without fear of cracking or breaking.
- Safe for Health:
- All products of Bat Trang ceramic undergo firing at very high temperatures, reaching 1250 – 1300 degrees, ensuring the complete elimination of lead and heavy metals that may exist in the clay.
- Quality Glaze:
- The glaze on Bat Trang ceramics is another significant characteristic. The fine, glossy, and deep nature of the glaze enhances the attractiveness of the products and prevents dirt from adhering during use.
- High Aesthetic Value:
- Another advantage of Bat Trang ceramic lies in its high aesthetic value, reflecting the essence of Vietnamese culture. Bat Trang ceramics come in various styles, glazes, and intricate patterns, carrying the distinct imprints of different historical periods and regions of the country. Bat Trang ceramics also exhibit a high level of creativity, constantly innovating and evolving to meet the demands of the domestic and international markets.
Bat Trang ceramic production process
To produce ceramics, ceramic artisans go through several steps, including selecting, processing, and blending clay, shaping the pottery, creating patterns, glazing, and finally, firing the products. The traditional wisdom passed down through generations in Bat Trang ceramic village is encapsulated in the saying, “First, the bone; second, the skin; third, the kiln.”
Ceramic artisans perceive the ceramic object as a living body, a miniature universe where the harmonious combination of the Five Elements (Ngũ hành) – metal (kim), wood (mộc), water (thủy), fire (hoả), and earth (thổ) – is crucial. The development of the craft is considered the flourishing manifestation of the Five Elements, and the prosperity of the Five Elements is intertwined with the creative labor process, involving precise and meticulous technical procedures.
The process of creating ceramic core
Choose land
The first crucial element in establishing pottery kilns is the source of clay for ceramic production. Ancient pottery production centers typically relied on local clay extraction. Bat Trang ceramic village is no exception. The residents of Bo Bat village chose the present-day Bat Trang area for settlement and ceramic development because they discovered white clay deposits here. By the 18th century, the local white clay deposits had been depleted, leading the people of Bat Trang to seek new sources of clay.
Unlike their ancestors, the people of Bat Trang chose to settle in strategically advantageous locations with convenient transportation, using boats to reach areas with new clay sources. From Bat Trang, they sailed upstream on the Red River to regions like Son Tay, Phuc Yen, crossed the Duong River, and traveled down the Kinh Thay River to Dong Trieu, exploiting white clay in Ho Lao and Truc Thon.
Truc Thon clay is highly plastic, water-resistant, fine-grained, and has a grayish-white color, with a firing resistance at around 1650°C. The chemical composition (average percentage by weight) of Truc Thon clay is as follows: Al2O3: 27.07; SiO2: 55.87; Fe2O3: 1.2; Na2O: 0.7; CaO: 2.57; MgO: 0.78; K2O: 2.01; TiO2: 0.81. While Truc Thon clay is favored by Bat Trang ceramic artisans, it has some limitations, such as a relatively high iron oxide content, significant shrinkage during drying, and it does not achieve a pure white color on its own.
Soil treatment and preparation
In the raw clay material, impurities are often present. Additionally, depending on the requirements of different types of ceramics, different clay preparation methods may be used to create suitable products. In Bat Trang, the traditional method of clay processing involves soaking the clay in a system of tanks, consisting of four tanks at different elevations.
The first tank, located at the highest position, is the “soaking tank,” used to immerse the raw clay and water (soaking time is approximately 3-4 months). Under the influence of water, the clay will break down its primitive particle structure, initiating the decomposition process (locally referred to as extended soaking to make the clay crumble). When the clay is “ripe” (as commonly called), it is uniformly beaten to make it soft, allowing the clay particles to truly dissolve in water, forming a liquid mixture. This liquid mixture is then transferred to the second tank called the “settling tank” or “filter tank.” Here, the clay begins to settle, and some impurities (especially organic substances) float to the surface and are removed.
Afterward, the diluted clay is scooped from the settling tank to the third tank called the “sun-drying tank.” Bat Trang artisans typically let the clay dry here for about 3 days, and then transfer the clay to the fourth tank, known as the “fermentation tank.” In the fermentation tank, iron oxide (Fe2O3) and other impurities are reduced through the fermentation process (meaning the microbial process of reducing harmful substances in the clay). The longer the fermentation, the better.
In general, the clay processing stage of Bat Trang ceramic artisans does not involve many complex steps. During the processing, depending on the type of ceramics, varying amounts of kaolin may be added.
Shape
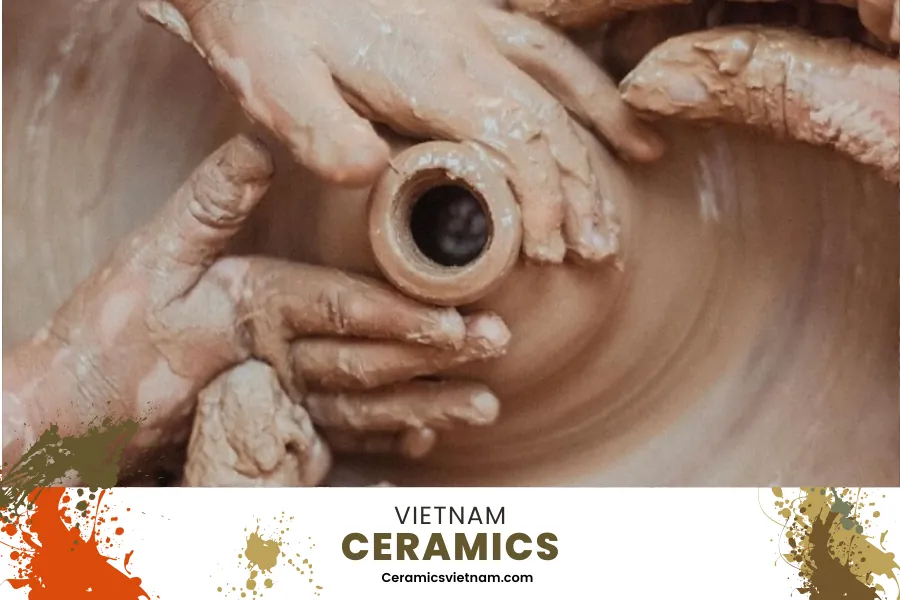
Advantages of Bat Trang Ceramic
The traditional shaping technique of the Bat Trang ceramic artisans involves handcrafting on a potter’s wheel. In the shaping process, Bat Trang ceramic artisans commonly use the method of “hand smoothing and trimming” on the potter’s wheel, a task that was traditionally undertaken by women. The artisan sits on a higher stool than the wheel, using their foot to rotate the potter’s wheel and their hands to shape the clay product. Before placing the clay on the wheel, it is kneaded until it becomes smooth, rolled into a coil, and then thrown (“springing”) to compact it. Subsequently, the clay is placed in the center of the potter’s wheel, tapped to ensure it adheres tightly, and then compressed and pulled to make the clay malleable, primarily using the right two fingers to “strike and lift” the clay.
After the manual and potter’s wheel shaping reaches the desired stage, the artisan employs a carving tool to refine and shape the product. Once the “trimming” and “cutting” are completed, the product is removed and placed in a “tray.” The initial shaping of the product using the potter’s wheel by women is a common practice in many traditional Vietnamese pottery studios (not just in Bat Trang) but may be unfamiliar to some Western ceramic artisans. However, this technique has gradually declined, and currently, very few Bat Trang ceramic artisans can still perform this task. “Trimming” is also a form of shaping on the wheel, usually done with a light touch, and is primarily undertaken by male artisans.
The artisans who “hand-build” ceramics possess high technical and artistic skills. Sometimes, they hand-build an entire ceramic product, while other times, they construct individual parts of a product and later assemble them. Today, according to the requirements of industrial or artistic ceramic production, ceramic artists can hand-build a prototype product for mold casting in plaster to facilitate mass production.
The process of shaping ceramics using molds (plaster molds or wooden molds) is carried out as follows: the mold is placed in the center of the wheel, securely pinned, the mold cavity is smoothed, and then the clay for the product is forcefully thrown into the mold cavity to adhere firmly. The clay is then scraped onto the edge, the wheel is rotated, and the roller is pulled to the necessary level to create the product. Nowadays, Bat Trang ceramic artisans commonly use the “casting” technique. To create a ceramic product using the casting technique, a plaster mold must first be made. Molds can range from simple to complex, with more complex molds having multiple parts, depending on the desired shape of the product. This method allows for the production of a batch of identical products simultaneously, making it quick and convenient. Additionally, the pouring and casting method is also employed: pouring “excess slurry” or a “full mold” to shape the product.
Drying and repairing wooden goods
The next step is to air-dry the raw products in a way that prevents cracking and maintains their original shape. The traditional and optimal method, still widely used in Bat Trang, is to let the items air-dry on racks in a well-ventilated area. Nowadays, many families opt to use drying ovens, gradually increasing the temperature to allow moisture to evaporate slowly.
Once the raw products are shaped, they need to undergo a “preliminary drying” process and be refined for completion. The ceramic artisan places the product on a table attached to a potter’s wheel and gently rotates the wheel while pushing the item lightly against a rib to provide support. They use a rib to gently press against the base of the product, making the clay adhere firmly and the product return to a round shape (referred to as “coaxing”). The ceramic artisan then performs various actions, such as cutting excess areas, filling in gaps, assembling parts of the product (such as spouts, handles, etc.), drilling holes, refining decorative patterns, and smoothing the surface of the product.
For products that are refined without using a potter’s wheel, it is called “handmade,” while those requiring a potter’s wheel are referred to as “wheel-thrown.”
Based on decorative requirements, additional clay may be added to certain areas of the product, and then cut and shaped (creating relief decorations). In some cases, deep patterns or decorations may be carved onto the surface of the product.
The process of decorating patterns and covering with enamel
Drawing techniques
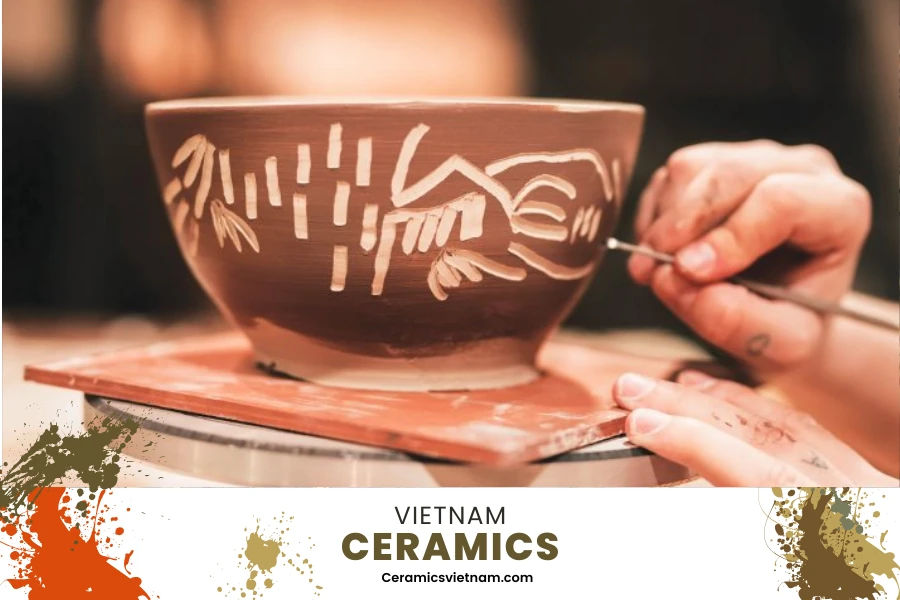
Advantages of Bat Trang Ceramic
Bat Trang ceramic artisans use brushes to directly paint intricate patterns on the raw ceramic surface. Ceramic painters must possess high craftsmanship, ensuring that the decorative patterns harmonize with the ceramic form. These artistic decorations elevate the ceramic craft to an artistic level, with each piece considered a unique work of art. Bat Trang ceramic artisans have also employed various decorative techniques, including embroidery, flowing glaze, and colored enamel painting, all contributing to the artistic effectiveness of their creations.
In recent times, there has been an emergence of new techniques in Bat Trang, such as painting on the glazed ceramic surface after the initial firing or the use of decal paper with pre-printed designs, imported from abroad. Although these techniques can produce visually appealing results, they are not considered part of the traditional Bat Trang heritage. Such methods are not regarded as artistic or creative contributions to the heritage of Bat Trang ceramics, and by extension, Vietnamese ceramics as a whole.
Making yeast
Iron glaze is a distinctive glaze in Bat Trang ceramics. In addition, there is also brown glaze, which includes iron glaze plus 5% rotten stone (a mixture of iron oxide and manganese oxide extracted from Phu Lang, Ha Bac). Since the 15th century, Bat Trang ceramic artisans have been known to produce a famous blue glaze. This glaze is made from red stone (containing cobalt oxide) and rotten stone (containing manganese oxide), finely ground and mixed with glaze. The blue glaze develops its color at a firing temperature of 1250°C. In the early 17th century, the people of Bat Trang used lime, rice husk ash, and the ash of Hoi Pagoda (located in Bich Nhoi, Kinh Mon, Hai Duong), which has a light pink color, to create a new type of glaze called crackle glaze.
Bat Trang ceramic artisans often use a wet glazing method, where finely ground and thoroughly filtered materials are mixed and stirred in water. After waiting for the mixture to settle, the water is removed from the top, and the sediment at the bottom is discarded, leaving only the suspended glaze particles in the middle – this is the shiny glaze layer used to coat the outer surface of the pottery. During the glaze-making process, Bat Trang ceramic artisans have observed that to make the glaze flow more easily, the processing of the fine powder of the ash must be much smaller compared to the clay powder. Hence, the saying “small ash, big glaze..
Enamel
Once the raw ceramic products are completed, ceramic artisans can either perform an initial low-temperature firing or apply glaze directly onto the finished raw products and then fire them. Bat Trang ceramic artisans often choose the direct glazing method on the finished raw products. Before glazing, the raw products must be cleaned of dust using a brush. If the ceramic bone has a color before glazing, a layer of glaze is applied to mask the color of the ceramic bone. Additionally, considerations must be made for the characteristics of each type of glaze applied to different ceramic bones, the glaze concentration, weather conditions, and the difficulty level of the ceramic bone.
The glazing technique has various forms, such as spraying glaze, pouring glaze onto the large-sized ceramic body surface, dipping glaze for small and common ceramics, and the most popular method is the “glaze tongs” where glaze is applied externally to the product. More challenging methods include “spinning glaze” and “casting glaze.” Spinning glaze involves applying glaze both inside and outside the product simultaneously, while casting glaze only applies glaze inside the product. These glazing techniques of Bat Trang ceramic artisans, serving as both technical and artistic methods, have been preserved through many generations and were once considered trade secrets in the craft.
Repair enamel goods
Ceramic artisans perform final adjustments to the products before placing them into the kiln. Firstly, they carefully examine each individual product to identify any areas lacking glaze, and if found, they apply additional glaze to those spots. Subsequently, they proceed with a “trimming” process, which involves scraping away any excess glaze. This task is commonly known as “glaze touch-up” or “glaze correction.
Burning process
- Kilns:
- Frog Kiln (Toad Kiln): The oldest type, shaped like a long frog, commonly used everywhere. Approximate dimensions: 7m long, 3-4m wide, 1.2m door, and a height of 2-2.7m. Five zones for stacking products inside.
- Dragon Kiln (Dan Kiln): Appeared in the mid-19th century, 9m long, 2.5m wide, and 2.6m high. Divided into 10 equal chambers. Temperature can reach 1250–1300 °C.
- Belly Kiln (Bau Kiln): Emerged in the early 20th century, divided into multiple compartments, usually 5-7, each with a rolling vault. The length is around 13m. Temperature can reach 1300 °C.
- Box Kiln (Vertical Kiln): Introduced around 1975 for family use, approximately 5m tall, built with fire-resistant bricks, simple structure, and fuel-efficient. Temperature can reach 1250 °C.
- Continuous Firing Kiln (Gas Kiln): Modern kilns like shuttle or tunnel kilns with gas or oil as fuel, allowing automated temperature control.
- Kiln Construction:
- Traditional kilns used square bricks for firing (famous Bat Trang bricks). Recent kilns use clay or clay mixed with crushed waste bricks for constructing the firing chamber.
- Kiln Loading:
- The stacking of products inside the kiln depends on the kiln type. For instance, in a dragon kiln, products are stacked from chamber 2 to chamber 10. Each kiln type has its own loading method to optimize space and fuel efficiency.
- Kiln Firing Process:
- The firing process involves gradually increasing the temperature until the ceramics are fully fired, then slowly lowering the temperature. The kiln master, often the most experienced artisan, monitors and controls the firing process.
- Traditional fuel includes straw, hay, bamboo, and later evolved to primarily using củi phác (preprocessed firewood) and củi bửa (kindling). Different kilns and products require specific stacking and fueling techniques.
- The cooling process takes several days, with the kiln being gradually opened and the products assessed and repaired if necessary.
- Clay Firing Container:
- Originally used square bricks for firing. Now, often made of fire-resistant clay mixed with crushed waste bricks.
- Fuel:
- For traditional kilns, various organic materials like straw, hay, bamboo, and later củi phác and củi bửa are used. For vertical kilns, than cám (rice husk charcoal) is the primary fuel.
- Loading Teams:
- The traditional loading teams were organized into three groups: bottom, middle, and top loaders. Each group had specific responsibilities during the loading process.
- Firing the Kiln:
- The firing process is challenging, requiring expertise in managing the fire. The dragon kiln firing takes about half a day, with a carefully controlled process of increasing fuel to achieve the desired temperature.
Characteristics of Bat Trang ceramics
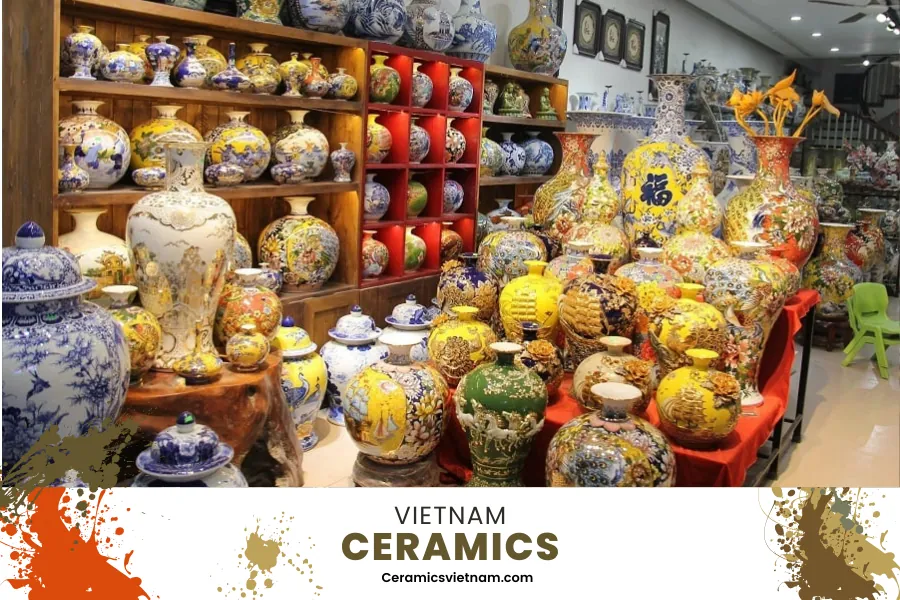
Advantages of Bat Trang Ceramic
Based on common characteristics related to bone structure, glaze color, decorative themes, and literary inscriptions, it is possible to identify key features of ancient Bat Trang ceramics.
Types of Ceramics:
- Most Bat Trang ceramics were handmade, showcasing the creative talent passed down through generations. Due to the manual shaping on a pottery wheel and the use of domestically sourced glazes, Bat Trang ceramics are known for their sturdy, dense, and relatively heavy structure. The white glaze often has an ivory hue. Bat Trang also has unique glazes, including jade-like glazes, brown and white glazes, and crackle glazes with a light brownish-gray ceramic base.
- Based on usage, Bat Trang ceramics can be categorized into:
- Household ceramics: Plates, flower pots, bowls, cups, trays, tea sets, pots, pipes, wine cups, vases, jars, funnels, and bottles.
- Ceramics for worship: Candle holders, candlesticks, incense burners, tops, altars, ceramic trays, and swords. Notably, items like candle holders and incense burners often contain inscriptions providing information about the author, place of origin, and manufacturing date, making them unique in Bat Trang ceramics.
- Decorative ceramics: Models of houses, dragon figurines, mythical creatures, Buddha statues, diamond statues, tigers, elephants, three-headed people statues, snake-bodied monkey head statues, and dragon statues.
Decoration Through the Centuries:
- 14th–15th Century: Decoration included techniques like engraved motifs, brown glaze painted in the Ly–Tran floral pottery style, combined with embossing and blue enamel painting. This period marked the emergence of the blue enamel floral pottery style, coexisting with brown floral pottery from the Tran period.
- 16th Century: Decorative techniques advanced, featuring refined embossing combined with blue enamel painting. Common themes included dragons, phoenixes, interweaving clouds, winged horses, human activities, standing lotus petals, floral vines, and landscapes. The use of blue enamel retained diverse geometric and floral patterns, resembling the Chu Dau floral pottery from Hai Duong province.
- 17th Century: Embossing and relief techniques became more sophisticated, resembling stone and wood carvings. New decorative themes emerged, including the Four Supernatural Beings, auspicious tigers, unicorns, and cranes. Embossed themes continued, with intricate patterns like oval lotus petals, eight-petal flowers, round lotus petals, square lotus petals, and Chinese characters “Van-Tho” (Hán characters). The use of blue enamel diminished, but decorative themes remained similar to embossing.
- 18th Century: Relief decoration became dominant, replacing blue enamel decoration on Bat Trang ceramics. Casting, assembly, and embossing techniques adapted to the use of single-color glazes (white-gray glaze and crackle glaze). New decorative themes included the Four Supernatural Beings, dragons, and symbolic plants representing the four seasons. Decorative patterns such as lotus blossoms, inverted lotus petals, and wave patterns became more prominent.
Leave a reply