Ceramics have a rich and enduring history, with their most significant advancements traceable back to the Ly Dynasty. In the present day, ceramics serve a dual purpose, not only as practical cookware but also as captivating pieces of art. The question then arises: how are these ceramic items fired using various types of ceramic kilns?
Traditional firewood kiln
The traditional firewood kiln, often associated with wood-fired pottery, holds the distinction of being the oldest and most time-honored kiln type in the world of ceramics. Crafted through a meticulous and delicate art, the process of wood-firing embodies the profound thought and boundless enthusiasm of the artisan. Each piece that emerges from this kiln carries not only unexpected but also deeply unique beauty, a hallmark that has garnered a dedicated following of enthusiasts for wood-fired ceramics.
Within the embrace of a wood-fired kiln, ceramics transcend the ordinary to reveal their fundamental and soul-stirring essence. It is here that the passage of time takes on a transformative role, acting as the pigment that imparts the distinctive colors and character to the pottery. This unique firing process gives rise to ceramics that exude a profound sense of quietude and authenticity, representing the very essence of what ceramics should always aspire to be.
On the whole, the traditional firewood kiln, with its time-honored techniques and remarkable outcomes, encapsulates the rich history and artistic depth of ceramics. It serves as a testament to the enduring allure of wood-fired pottery, where every piece is a masterpiece of both craftsmanship and nature’s influence.
Ceramic fired frog furnace
 Frog kilns, a relic of ancient ceramic heritage, once graced pottery-making regions across the globe. While their presence has dwindled in contemporary times, indirect sources allow us to envision the intriguing design of these unique kilns.
The frog kiln, aptly named for its resemblance to a frog, boasts dimensions of approximately 7 meters in length and 3-4 meters in width at its broadest point. Its height reaches around 1.2 meters, with a flat, horizontal base serving as the foundation for the ceramic firing process. Rising above, the kiln arch extends to a majestic height of 2 to 2.7 meters, imbuing the kiln with its distinctive character.
An essential feature of the frog kiln is the presence of a niche along its side, measuring approximately 1 meter in width and 1.2 meters in height. This niche serves a vital role in the stacking and unloading of ceramic products, facilitating the intricate firing process.
Though rare in contemporary ceramics, the frog kiln stands as a testament to the ingenuity of ancient potters. Its unique design and historical significance continue to capture the imagination of those intrigued by the rich tapestry of ceramic artistry through the ages.
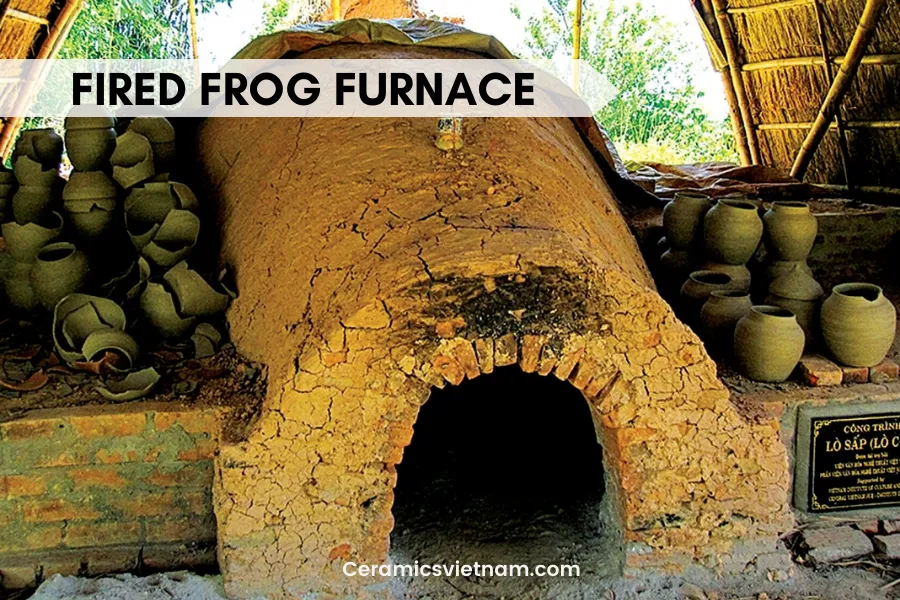
Ceramic fired frog furnace
Ceramic kiln
In the mid-19th century, a significant development unfolded in the world of ceramics with the introduction of a distinct type of kiln that showcased remarkable innovations in design and functionality.
This particular ceramic kiln spans an impressive 9 meters in length, measuring 2.5 meters in width and standing tall at 2.6 meters. What sets it apart is its unique structure, divided into 10 equal flanges, each separated by two columns. The kiln door, which serves as the portal to its inner workings, boasts dimensions of 0.9 meters in width and 1 meter in height.
Of particular note is the 10th flange, affectionately known as the “tofu flange.” This specialized section connects to a smoke collection chamber via three narrow doors, playing a crucial role in heat retention. To achieve this, the furnace flange extends and envelops the smoke collection chamber, a design innovation that enhances the efficiency of the kiln.
The inner wall of this kiln is meticulously crafted from Bat Trang bricks, renowned for their heat-resistant properties and suitability for ceramic firing. In contrast, the outer wall comprises civil bricks, providing structural integrity to the kiln’s exterior.
This mid-19th-century ceramic kiln stands as a testament to the ingenuity of its time, offering a glimpse into the innovative approaches that have shaped the world of ceramics. Its unique design and construction techniques continue to be of interest to those exploring the historical evolution of kilns and ceramic production.
Gourd oven, also known as dragon furnace
In the realm of ceramics, kilns have taken on diverse forms and functionalities throughout history. One such intriguing kiln type, which emerged in the mid-19th century, is worth a more in-depth exploration.
This particular ceramic kiln spans an expansive area, approximately 1030 square meters, with a length extending up to 15 meters. Its size alone reflects the ambition and scale of ceramic production during its era. Once the meticulously crafted pottery pieces find their place within the kiln, the potter embarks on a precise and patient journey.
The process commences with the potter sealing the kiln door, initiating a remarkable transformation that unfolds over the next 24 hours. During this time, the kiln’s internal environment undergoes a controlled, intense heat treatment, a pivotal step in the ceramic creation process.
After the 24-hour firing period, a critical waiting period ensues, allowing the kiln to gradually cool down. Patience becomes paramount as the potter anticipates the optimal moment to open the kiln and unveil the finished pieces, each a testament to craftsmanship and artistry.
The design of this kiln is a sight to behold. Its structure features five gourds, or consecutive arches, reminiscent of seashells, gracefully facing each other. This architectural arrangement serves both functional and aesthetic purposes, contributing to the efficiency of heat distribution and providing an artistic touch to the kiln’s exterior.
As we delve deeper into the world of ceramic kilns, this mid-19th-century masterpiece stands as a remarkable embodiment of the dedication, precision, and artistic vision that have shaped the evolution of ceramic production.
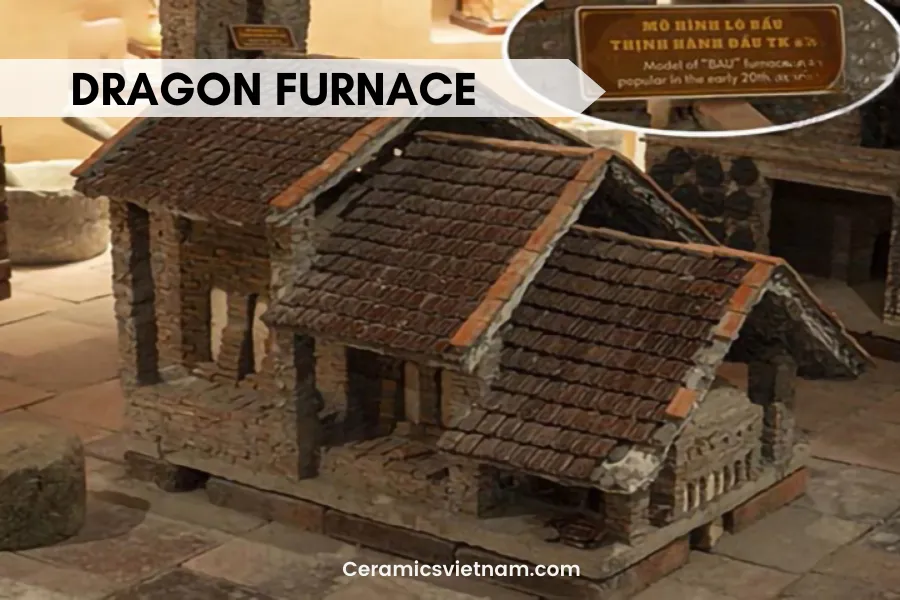
Gourd oven, also known as dragon furnace
Box-shaped ceramic kiln or vertical kiln
In the realm of ceramic kilns, the mid-20th century witnessed a notable addition to the family of kiln designs—the box furnace, also referred to as the vertical kiln. This innovation, which made its debut around 1975, brought about significant changes in ceramic production.
The box furnace is meticulously constructed using refractory bricks, resulting in a structure that stands approximately 5 meters in height and 0.9 meters in width. Its simplicity in design is one of its defining characteristics, featuring a box-shaped, vertical configuration that occupies relatively little space.
One noteworthy feature of the box furnace is its dual-door design, with one door at each end. This clever setup enhances the kiln’s efficiency by allowing for more straightforward loading and unloading of ceramic products. Additionally, the box furnace is particularly well-suited for small-scale production endeavors, making it a cost-effective choice for family-operated ceramic workshops.
In terms of temperature capability, the box furnace delivers impressive results, with an average temperature reaching up to 1250 degrees Celsius (or 2300 degrees Fahrenheit). This makes it suitable for a wide range of ceramic firing processes, ensuring that the desired results are achieved with precision.
When it comes to fuel, the box furnace primarily relies on wood and coal for its firing process. This combination of fuels provides both efficiency and affordability, contributing to the box furnace’s popularity among smaller production setups.
In brief, the box furnace stands as a remarkable innovation in the world of ceramic kilns, offering a compact, cost-effective, and efficient solution for ceramic production, particularly within family-operated workshops. Its introduction in the mid-20th century marked a significant milestone in the evolution of kiln technology and continues to be a valuable asset to the ceramics community.
Gas ceramic kiln
In the dynamic landscape of the ceramic industry, a significant breakthrough arrived in 2006 with the introduction of the gas furnace. This innovative kiln represents a notable step forward in both efficiency and environmental responsibility.
The gas furnace is a revolutionary type of kiln that has earned acclaim for its eco-friendly attributes. It stands apart from traditional kilns due to its remarkably reduced pollution levels, emitting no ash or smoke and generating very minimal dust during the firing process. This shift towards cleaner emissions aligns with the growing global emphasis on sustainability and reduced environmental impact.
One of the key advantages of the gas furnace is its impressive time-saving capabilities. Compared to traditional manual firing methods, such as using coal or firewood, the gas-fired kiln significantly shortens the time required to achieve the desired firing results. This time efficiency not only enhances productivity but also reduces energy consumption, making it a highly efficient and cost-effective choice for ceramic production.
Additionally, the gas furnace offers precise temperature control, ensuring consistent and predictable firing outcomes. This level of control is particularly crucial for ceramic artists and manufacturers seeking to produce high-quality pieces with minimal variations.
On the whole, the advent of the gas furnace in 2006 represents a pivotal moment in the ceramic industry’s evolution. This innovative kiln not only saves time and resources but also places a strong emphasis on environmental responsibility. Its clean-burning technology and precise temperature control have revolutionized ceramic production, making it a valuable asset for artisans and manufacturers alike.
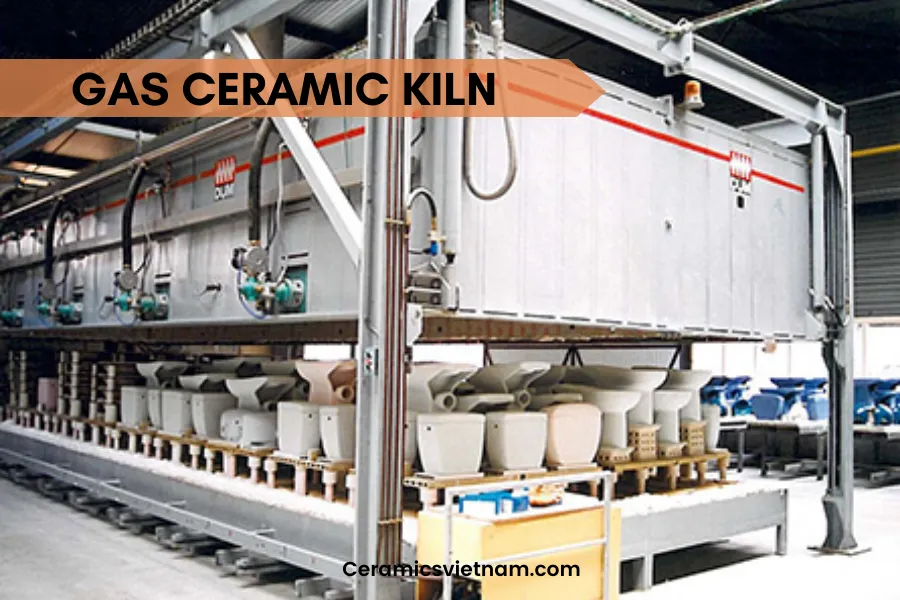
Gas ceramic kiln
Electric ceramic furnace
In the contemporary landscape of ceramics, electric kilns have risen to prominence as the preferred choice for the majority of enterprises and ceramic manufacturers. The shift towards electric kilns has brought about a multitude of advantages that have reshaped the way ceramics are crafted and fired.
One of the standout features of electric kilns is their precision in temperature control, facilitated by computerized systems. This level of control offers unparalleled convenience and accuracy, allowing artisans and manufacturers to fine-tune the firing process to achieve precise results consistently. This is a significant departure from older, manual firing methods, where temperature regulation was a far more intricate and labor-intensive endeavor.
The advantages of electric kilns extend beyond temperature control. They also contribute to substantial time savings during the firing process. Electric kilns eliminate the need for laborious fuel preparation and the management of combustion, leading to increased efficiency and productivity.
Another notable benefit of electric kilns is their reduced environmental impact. Unlike traditional kilns fueled by wood, coal, or gas, electric kilns produce minimal pollution. They emit no ash, smoke, or harmful byproducts into the environment, aligning seamlessly with contemporary sustainability initiatives.
Perhaps one of the most compelling reasons for the widespread adoption of electric kilns is the superior quality of ceramics they produce. The controlled, even distribution of heat ensures that ceramics are fired to perfection, resulting in pieces that not only meet but often exceed aesthetic and functional expectations. The consistency and predictability of electric kilns make them an indispensable tool for artisans and manufacturers striving to create top-tier ceramic products.
In conclusion, the prevalence of electric kilns in today’s ceramic industry signifies a transformative shift towards efficiency, precision, and sustainability. These kilns have redefined the art and science of ceramic firing, enabling the creation of superior, aesthetically pleasing ceramics that stand as a testament to the evolution of this timeless craft.
Read more
Leave a reply